Biofuels Industry
In the biofuels industry, agitators play a crucial role in various processes related to the production of biofuels from renewable resources. Biofuels are a type of alternative fuel derived from organic materials, such as crops, agricultural residues, algae, and waste materials. Agitators are used in several stages of the biofuel production process to aid in mixing, extraction, fermentation, and other critical operations. Here are the details of the use of agitators in the biofuels industry:
Biomass Pretreatment:
Agitators are employed in the pretreatment stage, where biomass feedstock is subjected to physical and chemical processes to break down complex organic structures. Agitators help in mixing the biomass with water or chemicals, such as acids or alkalis, to facilitate the breakdown of lignocellulosic materials into simpler sugars or fermentable compounds.
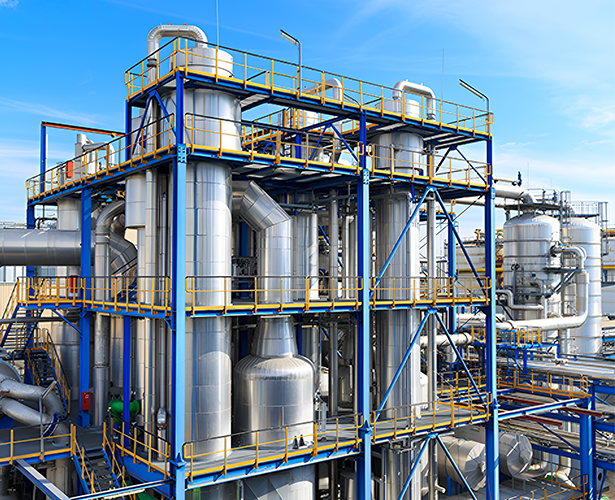
Hydrolysis:
In biofuel production, hydrolysis is a key step to convert complex carbohydrates in biomass into fermentable sugars. Agitators are used to mix the biomass slurry with enzymes (cellulases, hemicellulases) that catalyze the hydrolysis reaction. Effective mixing ensures the enzymes contact the biomass evenly, enhancing the conversion efficiency.
Fermentation:
Agitators are essential in fermentation processes, where microorganisms (yeast or bacteria) convert sugars into biofuels, such as bioethanol or biobutanol. Agitators provide adequate oxygenation and mixing, which are crucial for the growth and metabolism of the microorganisms. Proper mixing ensures uniform distribution of nutrients and helps prevent the formation of dead zones that can hinder fermentation.
Biodiesel Production:
Agitators are used in the transesterification process to convert vegetable oils or animal fats into biodiesel. The agitator ensures thorough mixing of the raw materials with alcohol (usually methanol or ethanol) and a catalyst (e.g., sodium hydroxide or potassium hydroxide). This promotes the chemical reaction that produces biodiesel and glycerin as a byproduct.
Algal Biofuels:
Agitators are employed in the cultivation of algae, which are used to produce algal biofuels. In algae bioreactors, agitators help maintain the proper mixing and circulation of the algae culture, ensuring uniform exposure to light, nutrients, and carbon dioxide. Proper agitation enhances algal growth and productivity.
Separation and Filtration:
After fermentation or hydrolysis, agitators may be used in separation processes to aid in the separation of biofuels from the fermentation broth or hydrolysate. They can assist in mixing and maintaining uniformity during centrifugation, filtration, or other separation techniques. Heat Transfer:
Agitators are employed in heat exchangers and reactors to facilitate heat transfer during various stages of biofuel production. For instance, they can help in cooling the reaction mixture during exothermic reactions or heating the feedstock during pretreatment.
Cleaning and Maintenance:
Agitators need to be regularly cleaned and maintained to prevent contamination and ensure reliable operation. The biofuels industry places high importance on maintaining hygienic and sterile conditions to avoid unwanted microbial growth and maintain product quality.
Scale-Up and Efficiency:
Agitators used in the biofuels industry must be scalable from lab-scale R&D to large-scale commercial production. Ensuring that the agitation process is efficient and reproducible is crucial to achieve consistent product quality and yield.
Overall, agitators are critical components in the biofuels industry, assisting in various steps of the production process to optimize yield, quality, and operational efficiency. Their precise and reliable operation contributes to the sustainability and viability of biofuels as a renewable and environmentally friendly alternative to conventional fossil fuels.
Pulp & Paper Industry
In the pulp and paper industry, agitators play a vital role in various processes, contributing to the efficient production of paper and paper products. Agitators are used to mix, suspend, and move pulp materials, chemicals, and additives during different stages of the papermaking process. Here are the details of their use in this industry:
Pulping Process:
Agitators are used in the pulping process, where wood chips or other raw materials are mixed with chemicals, such as sodium hydroxide and sodium sulfide, in a digester. The agitator helps ensure thorough mixing and uniform distribution of the chemicals throughout the wood chips, facilitating efficient cooking and delignification.
Bleaching Process:
Agitators are essential during the bleaching process, which aims to remove lignin and other impurities from the pulp to achieve the desired brightness and purity. Agitators are used in the bleaching towers to mix the pulp with different bleaching agents like chlorine, chlorine dioxide, hydrogen peroxide, or ozone. The agitator ensures proper contact between the pulp and bleaching chemicals, promoting effective and controlled bleaching reactions.
Mixing Additives and Chemicals:
Agitators are used throughout the papermaking process to mix various additives and chemicals with the pulp. These additives may include dyes, fillers, sizing agents, and retention aids. The agitator ensures even dispersion of these substances in the pulp, contributing to the paper's final properties and characteristics.
Paper Coating:
Agitators are utilized in the preparation of paper coating formulations. The agitator helps mix coating materials like pigments, binders, and additives to create a smooth and uniform coating that enhances the paper's surface properties, printability, and appearance.
Pulp Chests and Stock Preparation:
Agitators are used in pulp chests, which are large tanks that store and mix pulp before it enters the paper machine. Agitators maintain the consistency and uniformity of the pulp suspension, preventing settling and ensuring that the paper machine receives consistent feed.
Recycling and Repulping:
In recycling processes, agitators are used to repulp recovered paper and break it down into individual fibers. The agitator helps disperse water and chemicals within the repulping equipment, facilitating efficient fiber separation and removing contaminants.
Fiber Suspension and Flow Control:
Agitators are employed in various stages of the papermaking process to control the flow and consistency of the fiber suspension. Proper agitation ensures a consistent fiber distribution, which directly impacts paper quality, strength, and formation.
Chest Cleaning and Maintenance:
Agitators need to be periodically cleaned to remove any buildup of paper fibers, fillers, or chemicals that may impact their performance. Regular maintenance and cleaning are essential to ensure agitators operate at peak efficiency and prevent any potential process disruptions.